Navigating Industry 4.0 to transform manufacturing
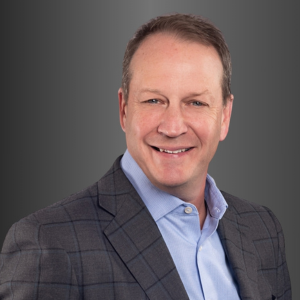
In the ever-evolving landscape of manufacturing, staying ahead means embracing change. One of the most significant shifts in recent years is the advent of Industry 4.0, also known as the Fourth Industrial Revolution or Manufacturing 4.0. As manufacturing businesses adapt to this digital transformation, understanding what Industry 4.0 entails and how it can be leveraged becomes crucial.
What is Industry 4.0
At its core, Industry 4.0 represents the integration of digital technologies into manufacturing processes, leading to a more interconnected, efficient and flexible production environment. This paradigm shift encompasses a range of technologies, including automation, artificial intelligence (AI), Internet of Things (IoT), cloud computing and data analytics. These advancements enable real-time monitoring, predictive maintenance and data-driven decision-making. Altogether, Industry 4.0 is revolutionizing traditional manufacturing operations, paving the way for smart factory industry 4.0 concepts and factory 4.0 implementations.
Why is Industry 4.0 important?
Industry 4.0 represents a fundamental shift in manufacturing, offering unprecedented opportunities for growth, efficiency and innovation. By embracing digital transformation in manufacturing and leveraging the power of data, manufacturing companies can unlock new levels of productivity and competitiveness in the global marketplace. The importance of Industry 4.0 digital transformation for manufacturing companies is evident in several key areas:
- Increased efficiency: Industry 4.0 technologies enable manufacturers to streamline operations and optimize employee utilization. Automated processes, real-time monitoring, and predictive maintenance minimize downtime and improve overall efficiency.
- Enhanced product quality: By leveraging data analytics and IoT sensors, manufacturers can gain deeper insights into production processes. This allows for better quality control, reducing defects and helping ensure consistency in product output.
- Cost reduction: Through automation and predictive maintenance, companies can lower operating costs associated with labor, energy consumption and maintenance. This leads to improved profitability and competitiveness in the market.
- Agility and flexibility: Industry 4.0 enables flexible manufacturing practices, allowing companies to quickly adapt to changing market demands and customer preferences. Digital technologies facilitate customization and personalized production at scale.
- Innovation and competitiveness: Embracing Industry 4.0 fosters a culture of innovation within manufacturing companies. By investing in advanced technologies and digital solutions, businesses can stay ahead of the curve and remain competitive in a rapidly evolving marketplace.
- Access to new markets: Digital transformation opens opportunities for manufacturers to expand their reach and enter new markets. Smart manufacturing capabilities enable remote monitoring and control, facilitating global operations and partnerships.
- Sustainability: Industry 4.0 promotes sustainable manufacturing practices by optimizing resource utilization, minimizing waste and reducing environmental impact. By embracing digital technologies, companies can achieve both economic and environmental sustainability goals.
- Future-proofing: In an era of rapid technological advancement, Industry 4.0 is essential for future-proofing manufacturing businesses. Companies that embrace digital transformation are better positioned to adapt to future disruptions and seize emerging opportunities.
Addressing manufacturing challenges
Industry 4.0 isn’t just about adopting new technologies; it’s about solving industrial challenges and IT challenges in the manufacturing industry in innovative ways. Manufacturers face a number of complexities, from crafting effective manufacturing strategies to achieving operational excellence, and smart manufacturing and automation can help businesses overcome barriers and unlock the full potential of Industry 4.0.
Challenge 1: Manufacturing strategy
- Data-driven decision-making: Industry 4.0 relies on data analytics and real-time insights to inform strategic decisions. By collecting and analyzing data from various sources, manufacturers gain a deeper understanding of market trends, customer preferences, and operational performance — allowing them to adjust their strategies accordingly. This data-driven approach enables more accurate forecasting and supply chain optimization.
- Flexible manufacturing: Industry 4.0 enables flexible manufacturing practices, allowing companies to quickly adapt to changing market demands and optimize production processes in real time. Flexible production systems and digital twins facilitate rapid prototyping and customization. This ensures responsiveness to market demands and helps in addressing cost challenges associated with traditional manufacturing methods.
Challenge 2: Operations excellence
- Automation and robotics: Industry 4.0 implementation and industrial automation 4.0 automate repetitive tasks and processes — reducing human error and improving operational efficiency. Robots and autonomous systems can handle tasks such as assembly, packaging and material handling — freeing up human workers for more complex and value-added activities. This shift requires careful change management and workforce reskilling to ensure a smooth transition.
- Predictive maintenance: By leveraging IoT sensors and predictive analytics, Industry 4.0 enables predictive maintenance. This detects potential equipment failures before they occur. It also minimizes unplanned downtime, reduces maintenance costs, and prolongs the lifespan of machinery and equipment. The integration of machine learning algorithms further enhances the accuracy of predictive maintenance models.
Challenge 3: Smart manufacturing
- Connected factory: Industry 4.0 creates interconnected manufacturing ecosystems where machines, systems, and processes communicate and collaborate seamlessly. IoT-enabled devices and sensors collect real-time data from the factory floor. This provides visibility into production activities, and it enables remote monitoring and control. The concept of a smart factory industry 4.0 or factory 4.0 relies heavily on this connectivity, often using 5G networks for high-speed, low-latency communication.
- Digital twin technology: Digital twins create virtual replicas of physical assets, allowing manufacturers to simulate and optimize production processes in a virtual environment. This enables predictive modeling, scenario analysis and continuous improvement — leading to higher productivity and quality. Digital twins are a key component of smart manufacturing industry 4.0, facilitating better decision-making and process optimization.
Challenge 4: Manufacturing automation
- Integration of robotics and AI: Industry 4.0 integrates robotics and AI into manufacturing processes, enabling autonomous decision-making and adaptive behavior. Collaborative robots (cobots) work alongside human operators — enhancing productivity, safety, and flexibility on the factory floor and allowing companies to appropriately use talent for high-value positions. This integration is a crucial aspect of industrial automation 4.0.
- Empowering the workforce: Industry 4.0 isn’t’ just about machines; it’s’ about empowering people. By leading through the transformation and providing training opportunities, manufacturers can help employees thrive in an advanced manufacturing environment. This focus on workforce reskilling is essential for successful industry 4.0 adoption.
Industry 4.0 is not just about the technology; it’s’ about advancing the people, processes and technology at a rate that provides a business a competitive advantage. Too much change or too fast change may not be sustainable. Therefore, a well-planned industry 4.0 implementation strategy is crucial.
Overcoming barriers for small manufacturing companies
While the benefits of Industry 4.0 are clear, small manufacturing companies often face unique challenges in adoption. Limited resources, lack of expertise, and concerns about data security and cybersecurity are common barriers. Our experts offer tailored Industry 4.0 solutions and advice to help small businesses navigate these challenges and thrive in the digital age. This includes guidance on legacy systems integration, ERP integration and the implementation of Industry 4.0 software solutions.
How Wipfli can help
Wipfli specializes in helping manufacturers get up to speed with Industry 4.0. Our team of professionals offers extensive industry knowledge, strategic guidance and actionable insights to navigate the complexities of digital transformation. We provide support for various Industry 4.0 use cases and help companies achieve significant productivity improvement and efficiency gains through smart Industry 4.0 practices.
Ready to embark on your Industry 4.0 journey? Learn more about how we can help you secure a competitive advantage.
Related content: