5 ways to improve job shop planning and efficiency
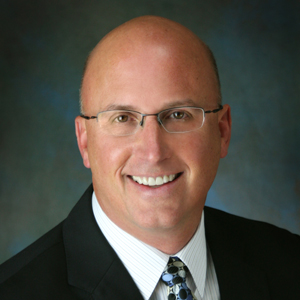
Job shops have to juggle multiple projects, custom requirements and a variety of lead times. High-mix operations are hard to optimize because of the variability from job to job. However, efficiency is critical to maintain lead times, protect profitability and win customers in a competitive market.
Your entire team needs to be working from the same playbook to operate at peak performance. Here are five ways to increase efficiency across the shop:
1. Evaluate and optimize your workflow
Before you can improve efficiency, you need a baseline. Measure your existing output today so you can set realistic goals for improvement.
Then, look at your workflows. Identify speedbumps and pain points that are holding you back. Maybe orders get hung up between sales and production. Or inventory runs dangerously low before it’s reordered.
Create a value stream map so you can see how materials and information should flow across the organization and then compare it to your current operations. Look for gaps in processes and other factors that delay operations. This exercise should include representatives from across the business so it captures the end-to-end journey, from order entry to arrival at the customer’s loading dock.
2. Get organized
Keep the shop floor (and other areas) organized to maximum efficiency.
Employees don’t have time to search for misplaced tools, supplies or files. Time is money. Plus, disorganization causes frustration and stress that lower morale.
Leading manufacturers apply the Lean or 5S methods to reduce waste and standardize
processes. Both originated in the Japanese manufacturing sector and focus on eliminating obstacles,
creating smoother workflows, preventing equipment failures, and using cleaning and maintenance schedules, among other procedures.
3. Evaluate equipment
Does your equipment spend more time in repair than it does in production? If so, you may need to reconsider its value to the organization.
Proactively evaluate each piece of equipment and its maintenance schedule. Once you start documenting maintenance, you may find that machines aren’t cleaned or lubricated often enough to operate at peak performance. Often, maintenance schedules can be adjusted to prevent issues — instead of waiting for an untimely problem to occur.
Software can help you measure output and monitor equipment performance over time. Sensors and meters can also tell you which assets are generating revenue and which ones are sinking the shop’s ROI.
4. Reduce work in progress
Unnecessary work in progress (WIP) significantly impacts job shop planning and efficiency.
Some WIP is typical, but too much ties up cash that could be earning higher returns elsewhere. WIP also takes up space on the shop floor and introduces unnecessary safety risks.
Figure out where excess WIP is coming from. It can result from improper production planning, manual labor, supply chain errors or other factors. Find the root cause of the problem(s) — then adjust your work plans to improve efficiency.
5. Use an ERP
Shops are too complex to manage manually, so departments adopt software to help them keep track of their work. Unfortunately, a lot of processes and systems are redundant. Sales uses one system, and purchasing relies on another. Instead of collaborating and sharing data, it gets locked in department-based silos.
Job shops need tightly aligned processes — and business information — to deliver complex orders on time. Every business unit needs to be connected and offered maximum visibility to work effectively.
An enterprise resource planning (ERP) system is an effective way to support shop operations. With one system, leaders and schedulers can pull the data they need to improve planning and lower the likelihood of errors. From there, they can maximize production, increase profitability and grow.
Once your shop is more efficient, you’ll find new ways to build competitive advantages.
How Wipfli can help
Efficiency doesn’t happen overnight. It takes commitment, plus the right processes, equipment and technology. Wipfli can help you find the perfect combination for your shop. Our manufacturing and technology specialists can help you explore the best workflows, processes and tools for your operation. Learn more.
Related content: