3 data solutions that give construction companies a competitive advantage
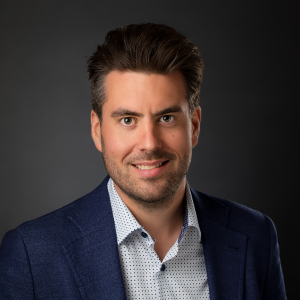
In the fast-paced construction industry, data-driven project management has become a game-changer for firms seeking a competitive edge. As construction projects grow in complexity, the need for efficient, strategic planning and decision-making has never been greater.
Construction firms are leveraging tools beyond their financial system, including field management tools, CRM and HRIS tools and, most notably, business intelligence tools to streamline operations, boost productivity and gain valuable insights into their projects and supply chains. Centralized data management, real-time project monitoring and supply chain optimization are helping construction firms improve their performance indicators and resource allocation.
These solutions can enhance compliance, risk management and overall project efficiency. By harnessing the power of data, construction companies can make informed decisions, adapt to changing market conditions and stay ahead of the competition.
Here’s how:
No. 1: Centralized data management
Centralized data management has become a necessity in the construction industry, replacing outdated methods of data storage and documentation like old-fashioned pen-and-paper reporting. This approach involves storing and managing all project-related information in a single, accessible location. It addresses common issues like inefficient labor allocation, miscalculation of job costs, project delays and conflicts due to miscommunication.
The benefits for construction firms are clear: automating tasks, reusing data and fostering a more productive workflow without disruptions. This approach streamlines training requirements, as employees learn one enterprise data model, fostering collaboration and understanding of roles across the organization.
With all critical data in one place, teams can maintain consistency and quality control, delivering a better customer experience and positive business outcomes. It enables real-time access to crucial information, allowing stakeholders to make more informed decisions whether they are on the job site or in the office.
Data integration strategies: To implement effective centralized data management, construction firms need to develop comprehensive data integration strategies. These strategies serve as blueprints for combining data from various sources to inform decision-making, boost operational efficiency and foster innovation.
The key steps to developing a successful data integration strategy are:
- Establishing concrete business goals.
- Documenting current and future-state business processes.
- Defining roles and responsibilities for key stakeholders.
- Choosing appropriate data integration tools and technologies.
- Crafting a structured plan for data flow between corporate systems.
The importance of data governance: Centralizing your data, both structured and unstructured, is only one part of the puzzle. To truly unlock value, that data needs to be properly governed. That means implementing frameworks to manage data security, privacy, compliance and overall quality throughout the integration process.
Effective data governance includes:
- Defining policies, standards and processes for controlling data access.
- Ensuring data security through encryption, authentication and backup measures.
- Monitoring key performance indicators related to data quality and system performance.
- Conducting regular reviews and assessments to identify areas for improvement.
By implementing robust data governance policies, construction firms can safeguard their data against unauthorized access, breaches and data loss while maintaining compliance with industry standards and regulatory requirements.
No. 2: Real-time project monitoring
Real-time project monitoring has become an essential tool for the construction industry, allowing firms to stay on top of the dynamic and complex nature of construction sites. This approach enables teams to track progress, identify issues and make informed decisions promptly, leading to improved project outcomes.
Collecting data in real time: Construction projects involve massive amounts of both structured and unstructured information, including BIM files, schedules, budgets and performance reports. Unfortunately, around 95% of this information often goes unused. Real-time data collection bridges this gap by providing up-to-date information from the field to the office.
Mobile field reporting plays a crucial role in this process. It allows on-site personnel, such as foremen, project architects and safety managers, to create reports and follow up with subcontractors more efficiently. This real-time approach helps ensure that all field teams remain on the same page and are fully prepared to start their tasks when the time comes.
Tracking key performance indicators: Key performance indicators (KPIs) are essential metrics used to measure a construction project’s success. They help project managers focus on a few valuable metrics that provide a clear picture of how a project and the business are performing.
Some critical KPIs include:
- Schedule compliance.
- Cost management.
- Quality metrics.
- Safety practices.
- Resource utilization.
- Customer satisfaction.
By tracking these KPIs in real time, construction teams can reduce delays, enhance visibility, make better decisions and improve accountability. This approach allows for the prompt identification of issues and adjustment of strategies to resolve problems before they cause significant damage.
Visualization tools: Data visualization has become an invaluable tool in construction project management. It simplifies the process of analyzing information, enabling stakeholders to act in a timely manner and make informed decisions.
Some common visualization tools include:
- Gantt charts, to understand project timelines and key milestones.
- Kanban boards, to monitor project movement from one phase to the next.
- Resource histograms, to show how personnel and money are allocated over time.
- Pie charts, to display the percentage of resources allocated to different activities.
- 3D models and heat maps, to identify risk areas on the job site.
These visual representations help project managers efficiently pinpoint areas where they may be over or underspending and take action sooner rather than later. They also aid in recognizing key milestones or constraints, making it easier to navigate project complexities in today’s hybrid work setups.
No. 3: Data-driven resource allocation
Data-driven resource allocation has become a critical factor in the construction industry’s quest for efficiency and competitive advantage. By leveraging advanced analytics and technology, construction firms can optimize their workforce, equipment and overall project performance.
Resource utilization analytics: Resource utilization is a key metric that measures the productivity of employees and teams over a specific period. It helps project managers identify under or overallocated resources, enabling them to make informed decisions about project planning, budgeting and scheduling.
The typical resource utilization formula is: resource utilization rate = busy time/available time.
This percentage shows how much of a team’s time is spent working. Construction firms can calculate resource utilization through comparing bookings or timesheets with team availability.
By using resource utilization analytics, construction companies can:
- Determine workload management policies.
- Predict future resource needs.
- Optimize capacity planning.
- Clarify the impact of future project bids.
Workforce planning: Effective workforce planning is essential for construction firms to maintain a skilled and efficient labor force. It involves analyzing current workforce supply and demand, forecasting future needs, identifying potential gaps and developing action plans to address any shortcomings.
To implement effective workforce planning, construction firms should regularly assess their current workforce with an eye toward the company’s future vision, while consulting with existing teams and employees and monitoring external factors like marketplace fluctuations.
Equipment optimization: Optimizing equipment usage helps construction firms minimize costs and improve project outcomes.
Key strategies for equipment optimization include:
- Implementing IoT-powered platforms for real-time data collection.
- Conducting regular inspections and preventive maintenance.
- Using employment schedules to track equipment usage patterns.
- Calculating accurate charge rates using total cost of ownership.
By leveraging these strategies, construction companies can:
- Improve equipment management practices.
- Minimize costs associated with equipment ownership and operation.
- Optimize equipment utilization.
- Enhance overall project efficiency and profitability.
How Wipfli can help
If your construction firm is looking to leverage a more data-driven approach to doing business, our consultants are ready to help you draw up the blueprints. Check out our e-book on calculating the return on your firm’s tech investments, and contact us to learn how you can leverage the data you already collect to gain a competitive advantage in an ever-changing industry.